«Treet» strekker seg mot Bergens regntunge himmel
I høst startet jobben med å bygge verdens høyeste trehus i Bergen. Selve bygget vil rage 51 meter til værs når det står ferdig en gang på seinsommeren 2015. Det er like høyt som Bergens stolte rådhus. Treet skal imidlertid ikke bygges. Det kommer som prefabrikkerte elementer i form av fiks ferdige leilighets-moduler fra Estland og banebrytende, spesialdesignet rammeverk i limtre fra Moelv.
– Målet for prosjektet har vært å gi bygget en arkitektur som tydelig formidler at dette er verdens høyeste trehus. Arkitektoniske grep har vært å binde sammen arkitekturen med konstruksjonsprinsippene. De åpne fasadene vil gi mye lys til leilighetene og omramme den fantastiske utsikten. For å beskytte bærekonstruksjonene i limtre vil bygget få innglassede balkonger på to sider. Dette vil gi bygget en helt særegen arkitektur, der limtrekonstruksjonene vil være synlige på innsiden av fasadeglasset. Gavlveggene blir foret ut og isolert. Dette gir mulighet for at prosjektet kan bygges som et passivhus, noe som ytterligere styrker prosjektets profil som et miljøbygg, sier Marina Trifkovic i Artec.
Bygg «Verdens høyeste trehus» selv, trinn for trinn på Bergen Tidenes hjemmesider.
Level fjorten
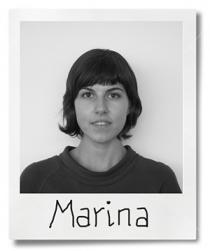
– Fordi den bærende konstruksjonen er på utsiden av bygget, må vi vite på millimeteren hvor hvert enste skråstag og fagverk står, kan vi tilpasse vegger - og alt som kommer inntil - helt nøyaktig. Hele bygget er av den grunn tegnet på millimeteren. Det er gitte avstander på alt. Når ventilasjonsrørene kommer ut på balkong, må de i noen etasjer bøyes for å unngå å treffe på et skråstag. Det hadde neppe vært mulig uten en åpenBIM-modell i og med at RIV- og RIB-modellen «kræsjer» i hverandre. I den felles IFC-modellen blir dette derimot tydelig og enkelt å forholde seg til, sier Trifkovic.
Øyeblikks-studier
En annen fordel med IFC-modellen er ifølge Trifkovic at det har vært mye enklere å oppdage feil, avvik og potensielle problemer. En ting teamet har gjort på et tidlig stadium er å simulere byggeprosessen gjennom en forenklet modell hvor de kunne slå av lag etter lag slik at man fikk visualisert det som skulle bygges i hver enkelt fase og på den måten delt opp hele prosessen.
– Denne funksjonaliteten brukte vi mye når vi skulle planlegge stillas og fuktsikring gjennom byggeprosessen, men også når vi skulle lage en tidsplan. Vi har rett og slett gått inn og tatt ut «frames» - altså bilder av gitte lokasjoner på i sine respektive faser - i byggeprosessen. Dette har forenklet byggeprosessen enormt og vi har kunnet planlegge detaljert, sett de forskjellige fasenes ulike utfordringer og identifisert potensielle problemer. For det er krevende sammenstillings-prosess i et veldig røft klima. Å bygge med tre i et ekstremt vått miljø krever at vi hele tiden må være forut for problemene. Det oppstår fort skader som er vanskelige å rette opp etter at de har skjedd, sier Trifkovic.
Montering for viderekomne
Trifkovic påpeker at monteringen foregår ved at fire ulike team bygger hver sin del. Deler som til slutt skal føyes sammen til en helhet. Først monteres fire leilighets-moduler oppå kjelleretasjen. Når de er montert bygges en bærekonstruksjon med en «poweretasje» - altså en forsterket plattform- i femte-etasje som monteres på bæresystemet av limtre. Tre som har ekstreme egenskaper. Ved å lime biter av tre sammen blir det minst like sterkt som stein eller betong.
– Det er avgjørende at de ulike delene kommer i riktige rekkefølge. Du kan se for deg et Lego-hus som settes sammen av fire ulike Lego-team med hver sin oppgave som skal løses hver for seg og som til slutt skal funke sammen. Derfor har vi byttet om mye på fasene ved å skyve rundt på våre «frames» for å finne en rekkefølge som får sammenføyingen til å gli glattest mulig, sier Trifkovic.
Spredt for alle vinder
Ved hjelp av øyeblikkstudiene i form av «frames» har man også kartlagt hvilke prosesser som kan foregå parallelt. I denne sammenhengen har IFC-modellen vært det foretrukne verktøyet fordi den er så presis, enkel og bærer i seg alle fagenes respektive modeller. Av samme grunn har også IFC-modellen blitt en sentral brikke i kommunikasjonen mellom fagene, de prosjekterende, byggherren og de spredte komponent-produsentene.
– Vi har brukt modellen flittig i alle de månedlige prosjekterings-møtene som gjerne går over en dag eller to. Modellen har på disse møtene blitt en fellesnevner som sikrer at vi snakker om de samme tingene og løser de samme problemene. Å være samkjørte til enhver tid er enklere sagt enn gjort når man sitter spredt for alle vinder. RIB’n har sittet i Lillehammer, Moelven Trelim på på Moelv og Kodumaja i Estland. På prosjekterings-møtene har vi samlet alle - i tillegg til alle utførende som er med i den aktuelle fasen - og løst problemene fortløpende. Det finnes omtrent ingen grenser for hva som lar seg løse når alle fag og bidragsytere sitter sammen. IFC-modellene har vært essensiell og helt uunnværlig i denne sammenhengen, sier Trifkovic.
Innflyttingsklare moduler
Den estiske produsenten Kodumaja leverer modulene så å si innflyttingsklare. På byggeplass kobles modulene sammen. Deretter er det bare tilkobling til el-, vann- og avløp som må fikses. Parallelt bygges korridorer, trappehus og heis. Lavere kostnader er bare en av to årsaker til at modulene hentes fra Estland. Transporten foregår med skip helt fram til byggeplassen i Bergen. Noe som verken hindres eller fordyres av sær-norske bestemmelser for brede og lange moduler på norske veier. Dessuten er det få norske leverandører som kan levere med samme grad av ferdigstillelse.
– I stedet for å prosjektere et bygg og få leverandøren til å tilpasse sine leveranser, har vi fått med oss leverandøren på prosjekteringen og laget ett bygg tilpasset leveransene. Dette har krevd mye i prosjekteringen og av kommunikasjonen mellom de utførende og de ulike komponent-produsentene. Prosessen har vært svært spennende og lærerik. Uten åpenBIM og IFC hadde det neppe blitt den samme suksessen. IFC har gitt oss en plattform å kommunisere på, et felles språk, en felles referanseramme. Det er jo ikke alltid det er like enkelt å skjønne hva RIB, RIE, RIV, RIA og RIBr snakker om, men i det øyeblikket objektene visualiserer seg i en modell skjønner «alle» instinktivt hva det snakkes om. Og det er jo rimelig uslåelig, avslutter Trifkovic.
Tekst: Morten Iversen
- - -
FAKTA OM «TREET»
• Verdens Høyeste trehus er en av brikkene i områdeplanen for Damsårdssundet. Bygget skal stå i vestenden av planen som det første bygget ved Puddefjordsbroen.
• Prosjektet har en ambisjon om å bli verdens høyeste trehus. Bygget skal utføres i sin helhet i tre, med en konstruksjon i limtre og leiligheter i moduler.
• Trehuset, slik det er tegnet, har 14 etasjer og 62 leiligheter. Ellve av de planlagte leilighetene er toroms mens resterende femtien er treroms.
• Leilighetene er løst med to moduler hver. For å gjøre produksjonen mest mulig effektiv var gjentakelse vektlagt. Bygget skal være areal- og kostnads-effektivt slik at det kan tilby rimelige leiligheter til unge mennesker som ønsker å bo bynært.
• Trekonstruksjonen til bygget er lagt på utsiden som en ramme og modulene er stablet inni. Modulene kan bare stables fire i høyden og på grunn av det ble det opprettet såkalte «poweretasjer» i hver femte etasje, slik at lasten fra fire og fire moduler blir tatt ut til søylene og ned til bakken.
• Prosjektets plassering er meget værutsatt og det kan være en utfordring for tremateriale å stå eksponert i slike omgivelser. For å beskytte trekonstruksjonen er det planlagt glassfasade i nord og sør og tette dobbeltfasader i vest og øst.
- - -
Hvem er med:
• BOB Eiendomsutvikling AS er byggherre.
• Rune B. Abrahamsen fra Sweco, Lillehammer, er fagansvarlig for konstruksjoner og bæresystemet.
• Kodumaja AS står som leverandør av byggmoduler.
• Arkitekt er Artec AS.
• Moelven Limtre står for produksjonen av limtrekonstruksjonene.
- - -
Fag: Arkitekt
Adresse: Damsgårdsveien 99
Oppdragsgiver: BOB
Areal: 4 600 m2
Status: Anbud
Skriv ny kommentar